The course assignment for LT2MEP/LT2306 Project Management, is to prepare a project plan for the purchase, installation and validation testing of a remote vehicle tracking system for a regional logistics company.
LT2MEP/LT2306 Logistics Tracking Project Assignment-Aston University UK.
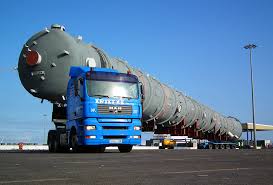
Background:
Eddy Barstow is a growing transport and logistics company, based in the Northeast region of the UK.The vehicle fleet consists of 42 semi-trailer tractor units, fitted with hands-free mobile radio for tractor-to-tractor and tractor-to-base voice communications and GPS navigation devices for
individual unit use. Barstow’s are seeking to improve operation efficiency and effectiveness through the use of a centrally coordinated route planning system. Several commercially available systems have been evaluated and a scalable system has been chosen as the basis for a fleet wide implementation.
The system selected will offer several benefits to Barstow’s, including:
1.Multi-drop route planning
2.Driver performance assessment (linked to bonus)
3. Optimized route planning for reduced fuel consumption and improved fleet CO2
4.Improved breakdown recovery tracking
5.Better planning for scheduled maintenance
Project Introduction:
Orbit IT has been contracted by Eddy Barstow to perform the installation and set up of the system across their fleet of vehicles. This includes final system specification, purchasing of the equipment, system trials, installation across 42 vehicles and training of operators. Barstow’s have asked for some unique data analysis features, which will require custom coding of proprietary software for the system. Orbit will develop the system as a turn-key installation and hand over a full functioning system after operator training. A technical support agreement will be in place for 30 days after hand over, to resolve any small issues or operational bugs.
Activity Constraints:
Orbit have been awarded the project and can begin working on the project from 12 th October 2020.The project should be handed over to Barstow’s (launch) no later than 2nd April 2021. If project activities extend beyond this date, Orbit will pay a project penalty of 2% of project value for each
working days delay.
(Note: There is an important activity constraint that has been missed from this description – What is it?).
Project Structure
The project can be broken down into four key activity areas for convenience:
Project Management: This area covers project planning, procurement activities, operator training,project handover activities and technical support. Project manager time can be allocated to this activity. It is anticipated that there will be a need for one full-time project manager to lead activities,for the duration of the project.
IT System Build: The system preparation and support covers system specification, software build,software updates and preparation of system operational manuals for reference once the program is handed over to Barstow’s personnel.
Vehicle Installation: GPS tracking units and driver displays will be required for each vehicle in the fleet. There will be a pilot installation to check out any issues with function, followed by a full fleet installation.
System Test: The system must first be developed on the workbench to evaluate function with hardware-in-the-loop. Once this breadboard testing has been completed, procurement of trial hardware can proceed. Electromagnetic compatibility checks will be completed on a first trial vehicle installation to ensure that there is no interference with vehicle safety systems, prior to the first vehicle trials. This will be undertaken in a specialist test lab. The final activity involved in testing will be the operational checks of the fleet roll-out (fleet validation).
Project Management
Project Planning:Project planning commences as soon as the project is approved (11th October 2020). This activity involves a software engineer for 20%, a purchasing agent for 15% and a hardware engineer for 10%
of the time, to draw up a detailed activity plan of all actions.
The planning activity should take approximately 4 days.
System Procurement
Purchasing activity will cover several phases of work.
LT2MEP/LT2306 Logistics Tracking Project Assignment-Aston University UK.
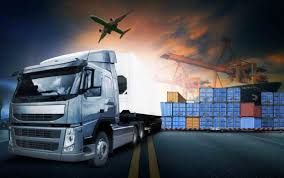
Initial Hardware Procurement: Purchasing of an initial batch of components will allow for first stage breadboard testing. This will require a Purchasing Agent working 30% of the time. Material costs are:
Vehicle GPS unit £280 each x 1 off
Pigtail wiring harness £65 each x 1 off
Vehicle display £185 each x 1 off
In addition, the GPS operating software licence must be purchased for the program as a single cost of £3,800 before any software development can occur.
Purchasing lead-time for the first components is estimated at 12-18 days, with an expected actual duration of approximately 14 days.
Trial System Procurement: Purchasing of the materials for the trial vehicle installation can commence after breadboard testing has been completed. Three vehicle systems will be procured, together with the equipment to set up the data centre facility at Barstow’s fleet operations office.This will require a Purchasing Agent working 30% of the time. Material costs are:
Data centre antenna unit £175 each x 1 off
Data centre server £3600 each x 1 off
Data centre display screens £160 each x 4 off
Data centre keyboard/mouse £80 each x 1 off
Vehicle GPS unit £280 each x 3 off
Pigtail wiring harness £60 each x 3 off
Vehicle display £185 each x 3 off
Purchasing lead-time for trial system components is expected to be 28 days. If parts are on back order, this could extend by an additional 10 days.
Project System Procurement: Once the vehicle trials have resolved minor issues with installation, procurement of the remaining systems can be completed, for the full fleet installation. Including spares, this equates to 39 off additional vehicle GPS units, pigtail wiring harnesses and vehicle
displays. Lead-time and costs for these parts is the same as the trial system components. Purchasing agent support is needed for 15% of this activity duration.
Operator Training: Before the operational system is handed over to Barstow’s data centre personnel and the fleet drivers can begin using the system, they require training in its operation and function.This will be carried out by one software engineer full-time and a hardware engineer working half-time. Training should take 2-4 days, but if issues are found, this may extend to 12 days.
Project Handover: After all installation and training has been completed, there will be a formal handover process to address any last minute issues or concerns. This will form the basis of the formal contract close-out. The activity will be supported by the project manager and a software
engineer for 30%. The event will occur over a 2 day period, unless issues are encountered, which may extend this activity to 5 days maximum.
IT System Build
System Specification: The system specification will start to be developed immediately after initial project planning is completed. This will involve a software engineer full-time and 30% of a hardware engineer. The task duration will be 3-6 days, but may be reduced to 2 days if work progresses
quickly.
Software Build: Specific data analysis coding will be programmed into the GPS tracking software that has been purchased for the program. This will take two software engineers 20-30 days to complete.
Software Updates: After pilot trials, there may be software update requirements to resolve unexpected issues. Six days has been allowed for this activity, but this may extend to 14 days if large problems are encountered. A software engineer will be available half-time for this activity.
Operations Manual Writing: Prior to training and hand-over, an operational manual for the entire system must be prepared. A dedicated period of 12-16 days has been allocated for manual preparation, using a software engineer, supported part-time (20%) by a hardware engineer.
Testing
Pilot Installation: Three vehicles will be used to test out fit, function and operation of the GPS system, prior to roll-out across the rest of the fleet. This work will be undertaken by a hardware engineer in one day. They will require use of the diagnostic tool during this period to resolve any
connection issues and have access to a £200 consumables budget for incidental expenses related to the installation.
Project System Roll-out: Full fleet installation can commence after operator training is completed.This will require the services of two hardware engineers, working full-time for 14 days. In the event of difficulties with installation, an additional two days may be required. A consumables budget of £300 for incidental installation expenses has been allocated to this task.
System Tests
Breadboard Testing: A prototype bench system will be build from the first batch of parts procured,to ensure component compatibility and resolve connections issues. This bench, or breadboard, test will be carried out by a hardware and software engineer over a five day period. Incidental
consumable required will be covered by a £50 budget.
EMI Testing: The first vehicle installation will require testing for electro-magnetic interference, to ensure that there are no vehicle operating concerns with engine or safety systems. This will require use of a specialist lab, at a cost of £2,500/day. A diagnostic tool will be required to interpret issues that may arise. A software engineer will support the test, which is expected to take six hours.
Pilot Functional test: A test of the pilot system can occur immediately after EMI testing is completed. This is required before software updates can occur. A full-time hardware and software engineer will be required for the duration of the test, together with a diagnostic tool. This task is anticipated to take 3 days.
Project System Validation Testing: This activity will occur on the fleet installation components immediately prior to installation in the vehicles. This requires a hardware engineer and software engineer full-time, with the services of a second software engineer using and diagnostic tool is
needed 50% to cover specific issue resolution. Total task duration is 4-6 days.
Technical Support: After project launch, there will be a period of 30 days of technical support for minor operational issues as Barstow’s personnel become familiar with the system and its operation.Orbit engineers available for this period are:
Project manager 10%
Hardware engineer 5%
Software engineer 15%
Task Dependency Logic
The dependency of tasks is a relationship between such that they may be required to be completed in a precedent order. An example of this is that the software build can only start after the system specification has been completed and must be finished prior to breadboard testing. By establishing
logical relationships of this sort, the overall timing of the project can be established.
It is advisable to establish dependencies on the project that are logically necessary, but care should be taken not to constrain the task more than necessary, as this prevents efficient levelling of resources.
Resources
Unless indicated otherwise, assume that human resource is allocated 100% for the duration of each activity.
Standard working week of 8 hr days x 5 day weeks apply. Overtime is not paid.
Total availability of resources and hourly rates are as follows:
1 Project Manager @ £92/hr
2 Software Engineers @ £80/hr
2 Hardware Engineers @£78/hr
1 Purchasing Agent @ £50/hr
Other expenses, such as project communications, travel, subsistence, incidental equipment, etc. are budgeted as a single estimate of £12,000. These costs are prorated over the duration of the project.
LT2MEP/LT2306 Logistics Tracking Project Assignment-Aston University UK.
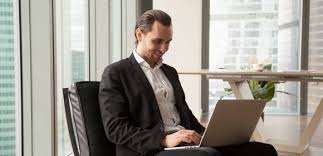
Charges for facilities are indicated in the task notes above and must be applied were used.
Specialist equipment and other incidental costs should be applied directly to tasks as they are used.
Note the project team has access to one diagnostic tool on a hire basis of £120/day.
A total budget of £250,000 has been allocated for this project.
Assignment Tasks
Project Plan
From the information provided above, draw up a Gantt chart timing plan, showing activity duration and relationships. Resources and costs are to be applied to each task. The plan is to be checked for viability for timing, cost and resource utilization i.e. ensure that there is sufficient resources available for each task, when required (no resource over allocation).
1.Construct a Work Breakdown Structure (WBS) that defines the major tasks to be completed,the precedent order of tasks and the appropriate ‘likely’ duration, based on the formula:
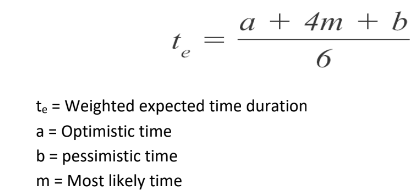
Make reasonable assumptions based on the information provided, stating your rationale for calculations and assumptions.
2.Define the relationship of the task to each other (dependencies). Draw arrows between dependant tasks, showing relationships. Be careful to appropriately constrain tasks by linking to achieve timing relationships, but do not over constrain, as this will lead to issues with resource levelling. Be careful not to have ‘hanging’ tasks that are not related to others,
as these will need to be manually adjusted when changes to the plan are made, such as resource levelling.
3.Assign resources to each task, based on the information provided, including human resource, materials, expenses, facilities etc.
4.Find the project Critical Path and highlight this on your Gantt chart.
5.Assess the plan for resource overloads (over allocation). Resolve any resource overload issues, noting what these were and how you addressed them.
6.Resolve timing issues by suitable means, potentially including rescheduling, reducing task duration, accepting risk or overtime working etc. Justify your choices, as appropriate. Note the imposition of any late penalties.
7.Ensure that the project meets to overall constraints of time, cost, resource limitations, etc. Summarize the project, including:
Final project plan start and end date
Overall project cost, including a breakdown of:
o Labour costs
o Components/parts costs
o Facilities costs
o Equipment hire charges
o Consumable expenses
o Other project expenses, including any penalties
Note, all costs must be accounted for. Provide a breakdown of what is included in each cost category.
- Any resource over allocation issues and how these have been dealt with in the final plan.
- Briefly comment on delivery risks with the project and how these have been accounted for or otherwise managed/minimized.
Project Plan Submission: You should find that the initial plan you develop using the information provided, has some challenges meeting overall constraints. You are expected to make reasonable adjustments of timing, resources and costs to meet constraints or otherwise manage risk.
You should clearly identify any issues encountered, State how you assessed these risks and what actions you took to manage these risks. Justify your decisions/adjustments.
A single document in Word format should be submitted via Blackboard. This should contain all the information to show your plan and the steps you took to come up with a viable plan. Make use of tables, charts and diagrams to explain your plan.
LT2MEP/LT2306 Logistics Tracking Project Assignment-Aston University UK.
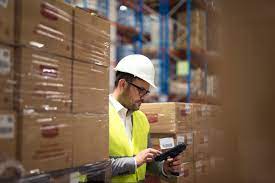
A word count of 3,000 words is allocated for this assignment. This is for guidance and is not a strict limit.
File naming convention is ‘Course code Surname Forename 2021’. The course code is either LT2MEP or LT2306 depending on your degree program. The date ‘2021’ refers to the academic year 20/21 and not the year 2021.
Marking Criteria
The following marking criteria should act as a guide for areas to be considered in the assignment:
10% Project Structure: Is the project plan logically structured, with a coherent work breakdown structure, including appropriate durations and relationships between tasks?
20% Task Definition: Are tasks fully defined, with resources, materials, facilities and costs associated for the completion of each task identified?
20% Resource Management (QCT): Are resources correctly calculated for each task and the project overall? Have resource over allocation issues been identified and addressed?
30% Risk Management: Has risk been identified for constrained resources on the project? Have issues been resolved and are the resolutions logical, justified and persuasive?
20% Overall Project Objectives: Does the proposed plan deliver the overall objectives of the project(timing, activities, resource utilization and costs)?
ORDER This LT2MEP/LT2306 Logistics Tracking Project Assignment NOW And Get Instant Discount
Read More :-